Following the certification of the SCHUNK SVH 5-finger hand, the SCHUNK Co-act EGP-C gripper has now also been DGUV certified for HRC operations by the German Social Accident Insurance. Why is certifying individual components so important for you, when it is actually the entire automated system as a whole that has to be certified for collaborative operation?
At our current stage, a large number of users are looking into HRC although only a few applications have been implemented into operational environments so far. The topic is relatively new for all the parties involved, which includes manufacturers of robots or end-of-arm tools and sensors, users, as well as the DGUV. Our experience shows that the path to certification can sometimes be challenging, especially for the first applications that do not have the benefit of experience. This is exactly what we are dealing with: we are supporting users with the interdisciplinary expertise of our SCHUNK Co-act team as well as minimizing the efforts involved in certifying entire systems with the help of our certified components.
Why is the certification process so complicated?
In order to get an entire automated system certified by the DGUV for HRC operations, it is necessary to ensure first that operators cannot be injured when it comes into contact. This is where the protection principles of DIN EN ISO 10218-1/-2 and DIN EN ISO/TS 15066 and the Machine Directive come into play, which stipulate that any hazards posed to humans and any associated risks must always be considered and assessed. That means it is important to make a very precise assessment of factors such as: what work spaces are present? What risks are involved? Where do work spaces have to be restricted in order to prevent injuries? This is only possible if each application is considered on an individual level: each component, task, workpiece, and security system. That simply takes time and careful attention.
Are there any safety concerns or fears with regard to grippers used in HRC applications?
So far we have not come across any great fears among users concerning grippers used in collaborative applications. On the contrary, there is actually a much greater sense of curiosity and enthusiasm – especially when it comes to intelligent systems such as the SCHUNK Co-act JL1 gripper. People see their encounter with the system as playful: they intuitively test out what triggers the safety technologies and how the system behaves. They start to gain confidence, which quickly dispels any fear associated with contact.
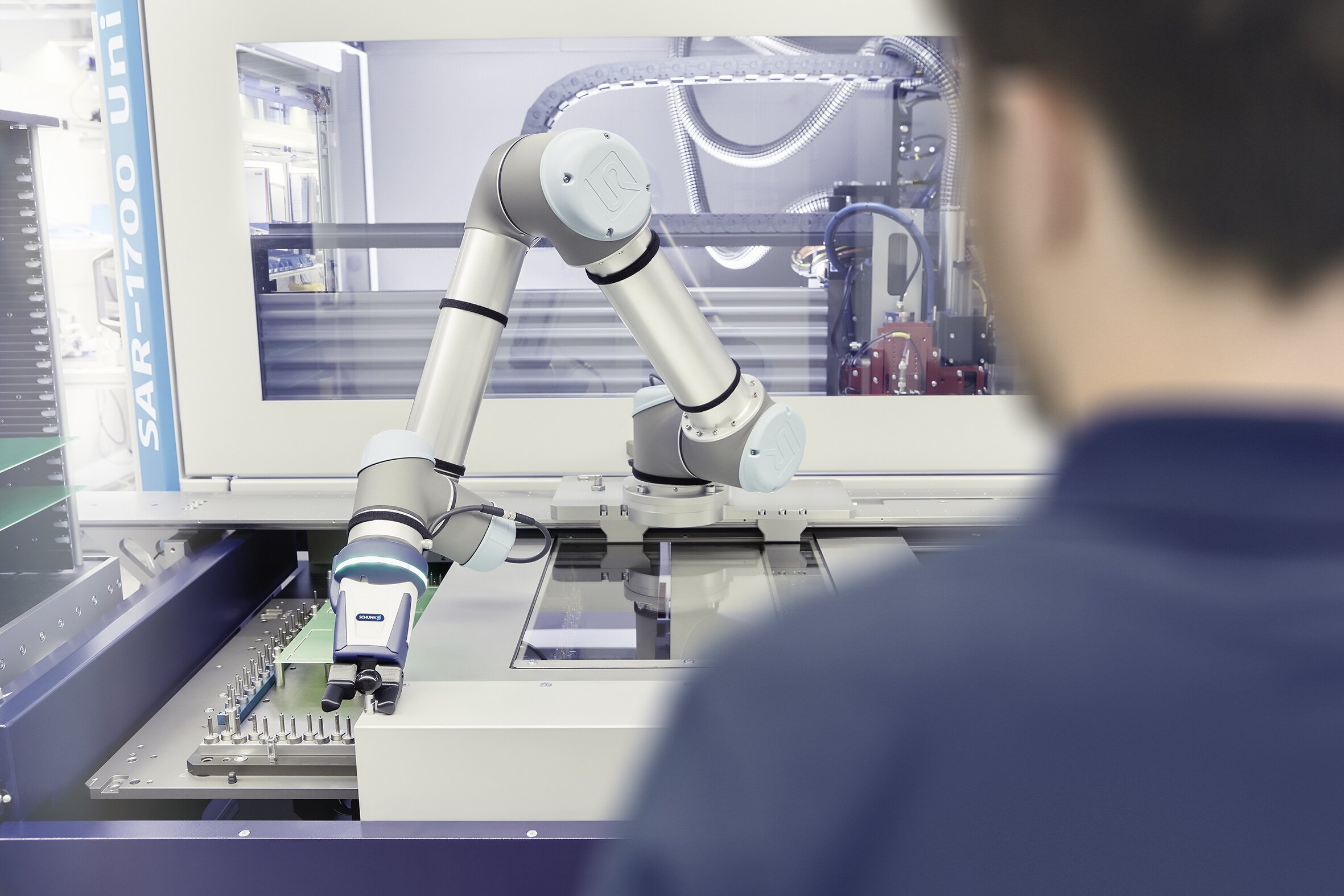
Teamwork in the electronics industry: With this depanelling machine, a robot arm equipped with SCHUNK Co-act EGP-C gripper supports the operator while loading.
Where does the challenge then lie?
Many aspects of human/robot collaboration are just as complex as humans themselves. Unlike conventional systems, simply meeting the standards is not enough. Firstly, standards only require that no serious injury or damage can be caused to the machine or the operator. However, this is not enough when it comes to daily use. Imagine if an HRC system were to bump into an operator 100 times a day. Even if this did not violate any standards, the system would have no chance of being accepted. It is much more important to make people, rather than the technical system, the main focus of all the considerations. The worker has to trust the robot. The gripper has to adapt to the human – not the other way around.
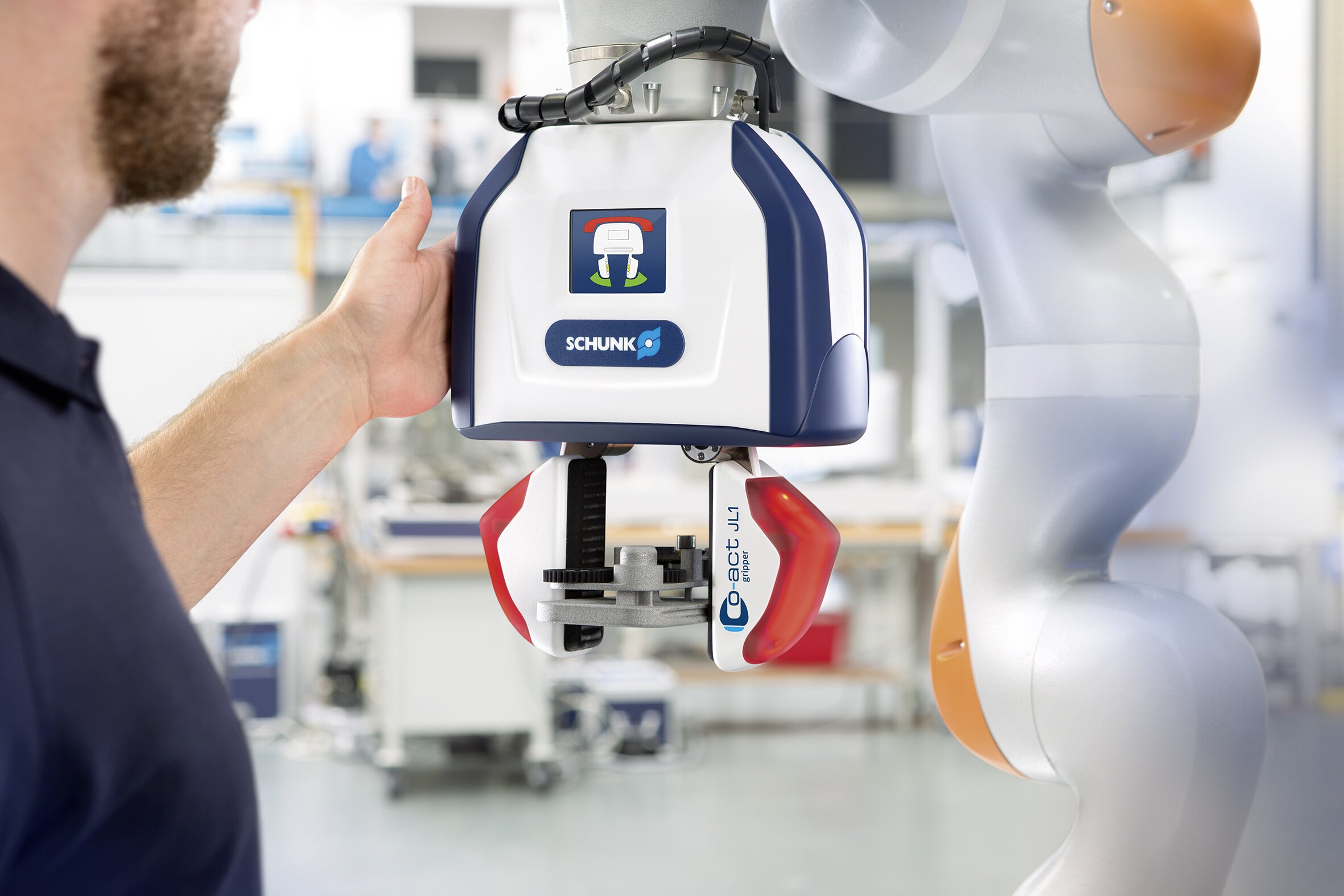
With the aid of tactile sensor systems in its fingers, the SCHUNK Co-act JL1 gripper is able to determine the absolute gripping force acting on an object. This makes it possible to ensure that fragile objects, as illustrated by this light bulb, are not crushed.
Doesn’t a gripper like this reach the limits of complexity?
Complex systems do not have to seem complicated nowadays. Take the smartphone: starting around secondary school at the latest, interacting with embedded technologies comes completely naturally to children: they write messages, surf the internet, watch films, photograph notes on the blackboard, make videos of experiments, make payments, or use their phone as a calculator, timetable or school agenda. They do all of this without thinking about how the device works. They just try out new apps intuitively, especially if their classmates show them first, and then they are practically already part of their standard app collection. This is exactly the scenario that we are pursuing with the SCHUNK Co-act JL1 gripper technology study: despite – or better yet – because of its complexity both inside and out, its use should be as intuitive as possible.
Can you describe the SCHUNK Co-act JL1 gripper safety aura in a little more detail?
The sensor technology installed in the SCHUNK Co-act JL1 gripper detects when humans are approaching and facilitates a reaction independent from the situation, without humans and robots coming into contact. It is divided up into three zones: each finger and the housing make up one zone each and can detect when a human is approaching independently of one another. This makes it possible for instance by successively triggering the sensor system in both fingers to determine the direction the human is approaching from, and use this information to determine an evasive movement of the robot immediately. Using the freely programmable controls integrated into the gripper, the corresponding reactions can be pre-processed and sent as a signal to the PLC. For example, it receives the command to reduce the speed by 25, 50 or 75 percent, or to stop. A pre-defined evasion strategy is even possible, as long as the direction of approach is clear. Each reaction mechanism can be defined individually and adapted to the corresponding application.
What technology is behind all of this?
Technically speaking, we use several systems in parallel: First, there is a capacitive sensor, this is, an electric field built around the gripper. As soon as something containing a lot of water enters this field, it is detected, for example a human hand. This makes it possible to distinguish between the approach of a component or another gripper, and the approach of fingers, hands or arms. In contrast to the established options on the market for work space monitoring, which generally cover a wider area, the capacitive sensor system makes it possible to immediately detect objects within a narrow radius of 20 cm, truly getting closest to the human before ever coming into contact. The second level is the force/torque sensors, which are installed in the flange. This registers the emergence of unexpected force effects. It detects an effective collision and stops the robot. In addition, it allows for additional functions to be realized, for example, we can determine whether a glass is full or empty. If and how workpieces are gripped. Tactile sensor systems represent the third level: Comparable with the human’s sense of touch, they sense spatially resolved individual contacts, but also large-scale pressure distributions. By means of intelligent algorithms for pattern recognition, objects are identified during the gripping process, and the grip can be reactively adjusted. This means that during the gripping process it can be recognized, if an object has been optimally gripped, or if a correction has to be done, also because, for example, if instead of an object a human hand has been gripped.
Where are we headed? What will grippers like the SCHUNK Co-act JL1 gripper be able to do tomorrow?
Specifically, there are two main aspects: assisting humans and alternating their handling of different kinds of components. With the help of specially developed gripping strategies, the sensitive SCHUNK Co-act JL1 gripper adjusts its behavior in real time depending on whether it is gripping a workpiece or a human hand. For this, the gripper uses a decentralized control architecture with diagnosis and safety functions carried out in parallel. In the long run, we believe that grippers, like human hands, will be able to independently manipulate the position and orientation of the gripped components in six degrees of freedom. In this connection, we talk about in-hand calibration technology. It will enable the realization of extremely flexible, autonomous gripping scenarios.
Source:SCHUNK