Okuma, offers state-of-the-art grinders that combine precision and productivity. The inner and outer diameter grinders possess multiple hardware and software solutions that make them exceptionally accurate, productive and reliable.
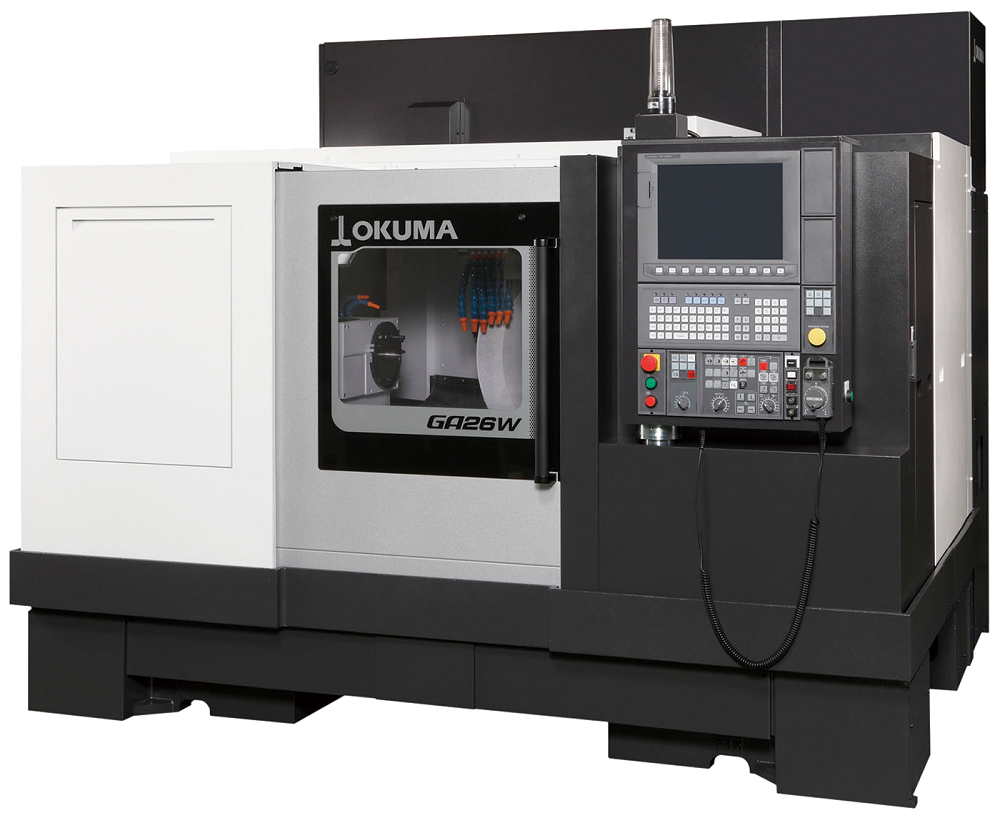
Okuma grinders such as the GA26W combine outstanding manufacturing quality with very high productivity. © Okuma
Since Okuma introduced its first grinder in 1918, the CNC machines have been improved constantly. Nowadays, Okuma offers highly advanced grinders that provide unparalleled accuracy and productivity. The machine tools are used in various industries such as the automotive sector or the aerospace industry where highly precise and extremely reliable grinding operations are required. Okuma’s innovative grinders for inside and outside diameter applications are suitable for both single piece production and highly automated mass production.
Innovative spindle design
With their highly stable construction, Okuma’s grinders offer extreme precision. The core of the machine tool is an advanced grinding spindle with an innovative three-point hydrodynamic bearing on the cylindrical grinders. This kind of wheel spindle bearing system supports the wheel with wedge-shaped oil film pressure that is generated by the wheel spindle rotation. This allows for a retention strength of one ton and a wheel rotation accuracy of 0.01 µm.
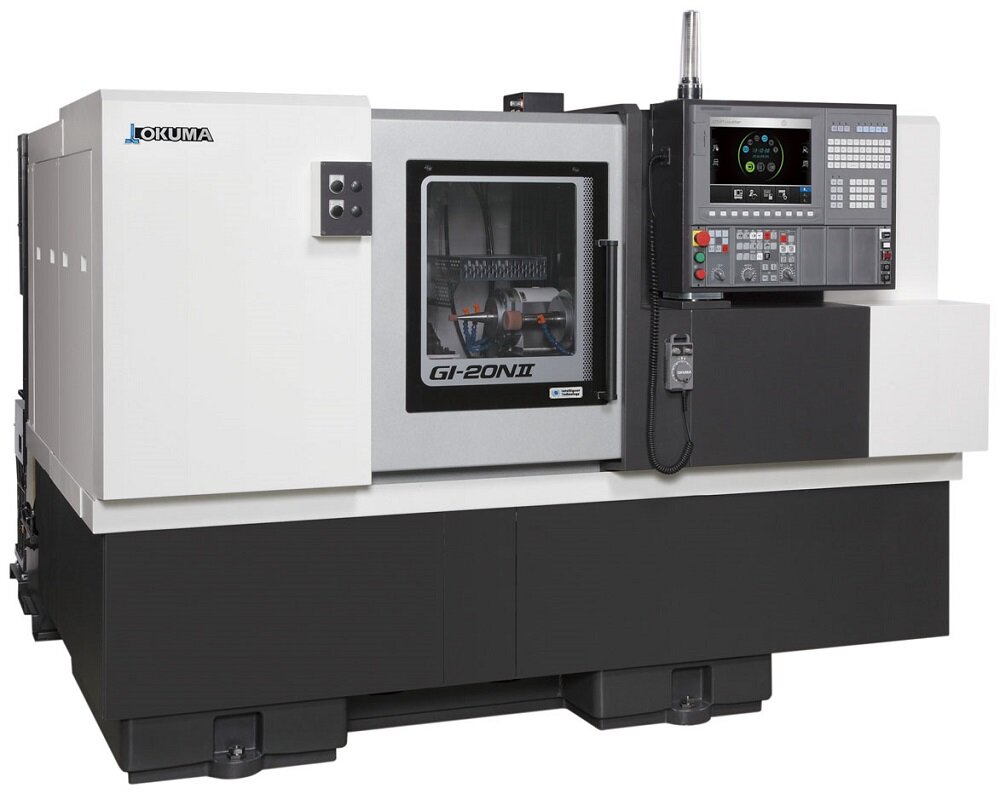
With the GI-20NII, Okuma offers a grinder for demanding inner and outer diameter grinding as well as for edge surface grinding. © Okuma
Uncompromised precision
The accuracy is maintained throughout the entire grinder. A robust 5-sided hydrostatic guideway offers highest reliability while achieving maximum follow-up accuracy on the internal grinders. With its wide distance between the two guideways, it holds vibration dampening properties. The grinder’s precision is further improved by Okuma’s Thermo-Friendly Concept which eliminates inaccuracies that occur due to thermal deformations. This makes tedious corrections and warm-ups obsolete and also renders the grinding process insusceptible to changes of the surrounding temperature.
Focus on productivity
Okuma grinders are extremely precise, and at the same time highly productive. They are equipped with multiple features that guarantee highest productivity under all production conditions. Outstanding rapid traverse speeds of 30 m/min allow for extremely short chip-to-chip times. The grinding process itself is designed as efficiently as possible. One example is the overlaying oscillation of the Z-axis which allows for higher removal rates and therefore shorter cycle times. This solution also improves surface roughness and is ideal for processing long workpieces.
Symbiosis of electronics and hardware
As the industry’s only single-source provider, Okuma also manufactures the grinder control OSP-P300GA. The Windows-based control relies on an open architecture making it extremely easy to be integrated into any workshop environment. The programming itself is an easy dialogue-supported cycle programming. With its intuitive design, Okuma reduced the required manual inputs to a bare minimum. This makes the grinding process both ergonomic and highly productive. The OSP additionally shields the grinding process from blackouts and other interruptions as it uses an absolute positioning system.
Source:OKUMA