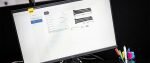
Web users can customize tools using new online service
CoroBore BC from Sandvik Coromant is easier to order and less expensive than engineered tools.
Two new drills optimized for drilling aluminium automotive parts have been developed by cutting tool and tooling systems specialist Sandvik Coromant. Ideal for the machining of components in medium-to-large volumes, CoroDrill® 400 and CoroDrill 430 deliver higher throughput and lower costs, as well extended tool life and enhanced process security.
Sandvik Coromant adds thinner grooving insert to CoroCut® 1-2 programme
A decision has been taken to open a new Sandvik Coromant Centre in Renningen, Germany that will include a showroom, training facilities, and a design and project office. Sandvik Coromant Centres are world class facilities for productivity, applications, machining and research in manufacturing. In Renningen, the team will focus on the automotive industry.
CoroCut® QF is a new concept from cutting tool and tooling systems specialist Sandvik Coromant that has been developed exclusively for face grooving. Designed to deliver unmatched reliability and superior process security, even when machining deep and narrow face grooves, CoroCut QF also provides enhanced accessibility to awkward features.
Following last year’s launch of PrimeTurning™ methodology and tools for external turning operations, Sandvik Coromant is now introducing a dedicated CoroTurn® Prime SL head that makes this groundbreaking process available for internal turning operations. The new SL head will cater for the needs of oil and gas, aerospace and other manufacturers machining diameters in excess of 90 mm (3.5 inch), and overhangs up to 8-10xD.
The CoroThread® 266 thread-turning tool from Sandvik Coromant is available from 1st March 2018 with precision over- and under-coolant to improve process security and maximise efficiency. The addition of over-coolant improves chip formation for more secure machining, while under-coolant controls temperature for long and predictable tool life. Precision coolant also has positive effects on surface finish, further supporting the generation of high-quality threads.